メッキは幅広く、
加工の過程で電気を使う電気メッキと
使わない無電解メッキの大きく2種類にわけられます。
我々が扱う溶融亜鉛メッキは後者にあたり、工業製品をサビから守ることをメインに置いています。
皆さんが普段見かけるガードレールや街頭のポール、マンションの外階段といったものは、
すべて溶融亜鉛メッキで下処理がされた上で、ペンキやコンクリートなどで塗装されています。
そして、溶融亜鉛メッキの良点は、
扱いが簡単なこと。
耐久性が優れ、市街地なら50年、海沿いでも10年サビから守ってくれます。
あちこちで多種多様に使われていますが、
人目にはつきにくい…まさに、縁の下の力持ちと言えるでしょう。
溶融亜鉛メッキの特徴と利点
塗装と溶融亜鉛メッキとの違い
溶融亜鉛メッキと比較されることが多いのは、塗装です。
塗装の利点は、色が選べる事と種類が豊富なこと、外観が綺麗なことです。
しかしながら、塗装と溶融亜鉛メッキとの防食性能は雲泥の差があります。
塗装は4〜5年に一度再施工しないと防食性能は持ちません。
さらに数年年月が経過すると、色あせなどがおこり見た目も変わってきます。
傷にも弱く塗装面に傷があるとそこからサビが起こり母材(塗装の下の鉄)を侵食します。
溶融亜鉛メッキは「保護皮膜作用」と「犠牲防食作用」という2つの大きな特徴があります。
-
- サビに強い「保護皮膜作用」
-
亜鉛メッキの表面にできる亜鉛の酸化被膜が、空気や水を通しにくい安定した性質を持っているためサビを防ぎます。
この特徴は、一般大気中や、水中・土中・コンクリート中においても発揮されます。
-
- キズに強い「犠牲防食作用」
-
鉄鋼製品の表面に施された亜鉛メッキ被膜は外部の腐食環境より鉄鋼製品を保護する保護被膜となります。
そのため亜鉛メッキに、万一、キズが発生し、素地の鉄が露出したとしても、電気化学作用(ガルバニックアクション)によりキズの周囲の亜鉛が犠牲になり、鉄より先に溶け出して、鉄を腐食させません。
溶融亜鉛メッキ5つの利点
- 1 優れた密着性
- 溶融亜鉛メッキは、他の塗装と違い鉄素地と亜鉛の合金化反応により密着しておりますので、過激な衝撃や摩擦以外に剥離することはありません。
- 2 剥離しにくい
-
溶融亜鉛メッキのメッキ皮膜は、鉄と亜鉛の合金層ができるため、鉄素地との密着性が良好です。
一般的な取り扱い方法では、衝撃・摩擦などによって剥離することはありません。
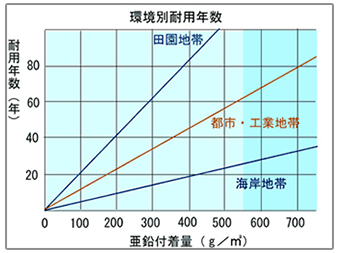
- 3 経済性に富む
- 長期間にわたって防食効果がありますので、(環境により地域差があります)補足的な防食手段はほとんど必要ありません。理論的には、表面の亜鉛メッキ層が電気化学作用により完全に消耗されつくすまで鉄鋼製品を錆から守りますので、長期の防食を目的とする場合、他の防錆法と比較して最も経済的な方法です。
- 4 様々なサイズでメッキが可能。
-
メッキ槽に浸漬することが可能な鉄製品は、すべてメッキが可能。
弊社のメッキ槽は様々なサイズに対応でき、最大11メートルに及ぶ大型製品までメッキ加工できます。 - 5 どんな形でもメッキが可能
-
手の届かない部分までメッキが可能なのが、溶融亜鉛の利点です。
たとえば、細長い管のようなものであったり、中空体などであっても溶けた状態の亜鉛が出入りすることができるのであれば、均一にメッキをすることが可能なのです。
溶融亜鉛鍍金の規格
JIS H 8641 溶融亜鉛メッキ規格
横スクロールできます
膜厚と付着量との関係 | |||
---|---|---|---|
素材の厚さ | 種類の記号 | 膜厚 μm | 付着量 g/㎡ |
厚さ1mm以上の素材、直径12mm以上の ボルト・ナット及び厚さ2.3mmを超える座金 |
HDZT 49 | 49以上 | 350以上 |
厚さ2mm以上の素材 | HDZT 56 | 56以上 | 400以上 |
厚さ3mm以上の素材 | HDZT 63 | 63以上 | 450以上 |
厚さ5mm以上の素材 | HDZT 70 | 70以上 | 500以上 |
厚さ6mm以上の素材 | HDZT 77 | 77以上 | 550以上 |
- <備考>
-
- 1. 表中適用例の欄で示す厚さおよび直径は、公称寸法による。
JIS H 9124 溶融亜鉛メッキ作業標準
JIS H 0401 溶融亜鉛メッキ試験方法
- その他、溶融亜鉛メッキ製品の規格として、次のような規格があります。
-
- ・JIS H 2107 亜鉛地金
- ・JIS G 3302 亜鉛鉄板
- ・JIS G 3442 水道用亜鉛メッキ鋼管
- ・JIS G 3532 鉄線
- ・JIS G 3534 亜鉛メッキ鉄より線
- ・JIS G 3537 亜鉛メッキ鋼より線
溶融亜鉛メッキの加工の工程
溶融亜鉛メッキがどのように加工されているのか、当社における工程をご紹介します。

仕組みの工程
鋼材を前処理工程に進めるため、様々な種類の治具を用いて形状・数量・規格に応じた最適な形に組みます。
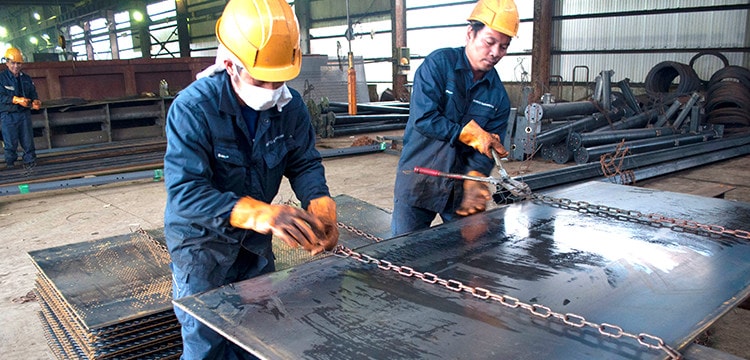
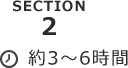
前処理工程
- 脱脂槽
- 仕組み工程で組んだ鋼材を脱脂液に入れ、表面に付着している汚れ・油分を除去します。
- 塩酸槽
- 脱脂後の鋼材を塩酸に入れ、素材表面のミルスケール(酸化被膜)を落とします。被膜が残っている箇所では亜鉛との合金反応が起こらず不メッキとなるため、完全に除去できるまで塩酸に漬け、鉄の素地を露出させます。
- フラックス槽
- 塩酸の後はフラックスに入れ表面を被膜で覆うことで、メッキまでの少しの時間鋼材の表面に錆が発生するのを防ぎます。加えてフラックスに浸漬することにより、鉄と亜鉛の合金反応を促進します。
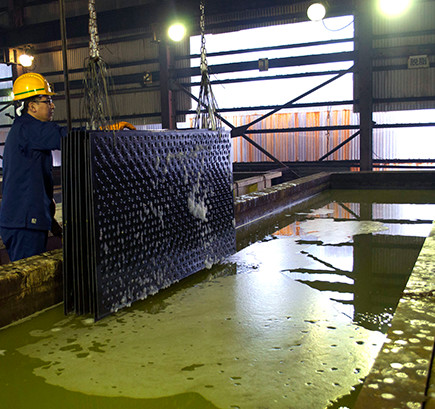
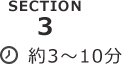
メッキ工程
- メッキ槽
- フラックス処理後の鋼材を、440℃程に熱して溶解したメッキ槽に入れます。鋼材の表面に鉄と亜鉛の合金層が形成され、強い防錆力を発揮します。
- 冷却水槽
- メッキ後の高温になった鋼材を水に入れて冷まします。曲がりやすい形状の鋼材は、一度空冷してから冷却水に入れます。
- 白錆防止槽
- 最後に白錆防止槽に鋼材を入れ表面に被膜を形成することで、一時的に白錆が発生しにくくします。
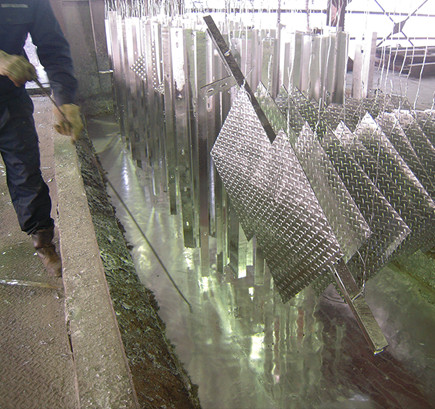
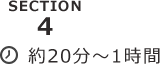
仕上げ
鋼材の外観をチェックし、不メッキ・鋭利なタレ・ざらつきなどを工具により仕上げ、必要な個所に補修を行います。
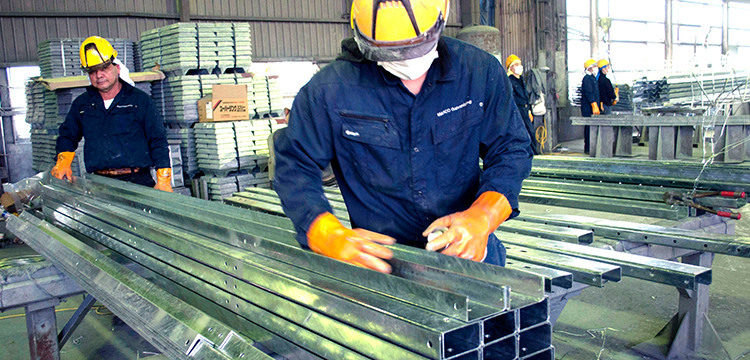

膜厚検査&外観検査
仕上げ後の品物の外観検査を行うと共に、専用の器具を使いメッキの付着量が規準値を超えているか検査します。

計測
仕上げ後の鋼材の外観チェック・数量チェックを行うのに加え、台貫にて重量を計測します。
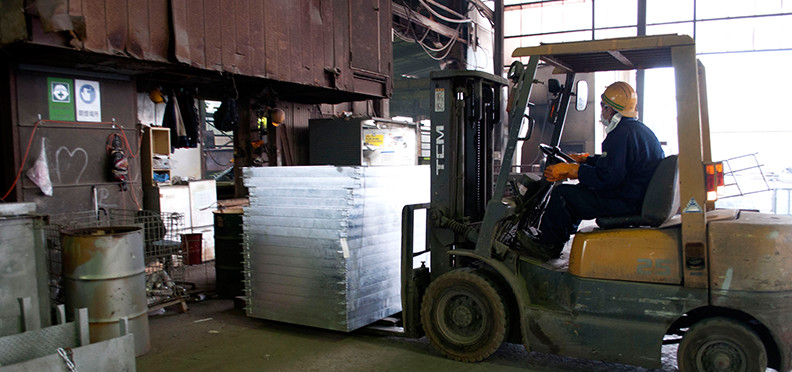

仕組みの工程
鋼材を前処理工程に進めるため、様々な種類の治具を用いて形状・数量・規格に応じた最適な形に組みます。
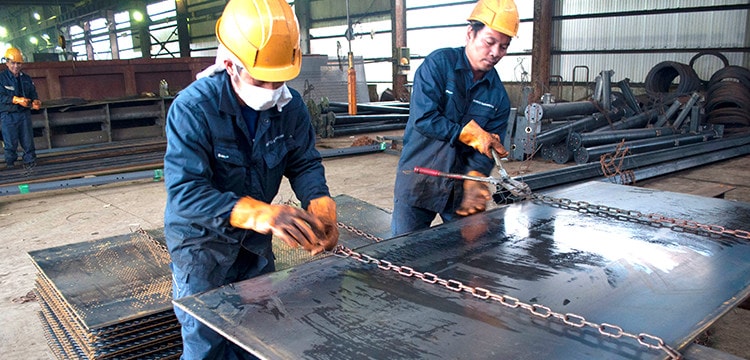
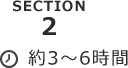
前処理工程
- 脱脂槽
- 仕組み工程で組んだ鋼材を脱脂液に入れ、表面に付着している汚れ・油分を除去します。
- 塩酸槽
- 脱脂後の鋼材を塩酸に入れ、素材表面のミルスケール(酸化被膜)を落とします。被膜が残っている箇所では亜鉛との合金反応が起こらず不メッキとなるため、完全に除去できるまで塩酸に漬け、鉄の素地を露出させます。
- フラックス槽
- 塩酸の後はフラックスに入れ表面を被膜で覆うことで、メッキまでの少しの時間鋼材の表面に錆が発生するのを防ぎます。加えてフラックスに浸漬することにより、鉄と亜鉛の合金反応を促進します。
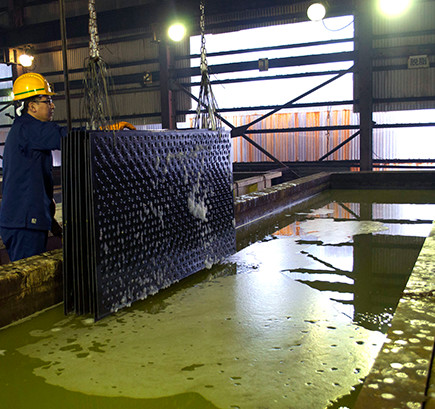
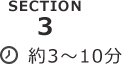
メッキ工程
- メッキ槽
- フラックス処理後の鋼材を、440℃程に熱して溶解したメッキ槽に入れます。鋼材の表面に鉄と亜鉛の合金層が形成され、強い防錆力を発揮します。
- 冷却水槽
- メッキ後の高温になった鋼材を水に入れて冷まします。曲がりやすい形状の鋼材は、一度空冷してから冷却水に入れます。
- 白錆防止槽
- 最後に白錆防止槽に鋼材を入れ表面に被膜を形成することで、一時的に白錆が発生しにくくします。
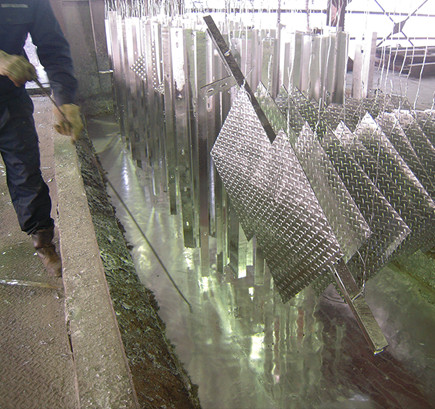
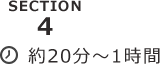
仕上げ
鋼材の外観をチェックし、不メッキ・鋭利なタレ・ざらつきなどを工具により仕上げ、必要な個所に補修を行います。
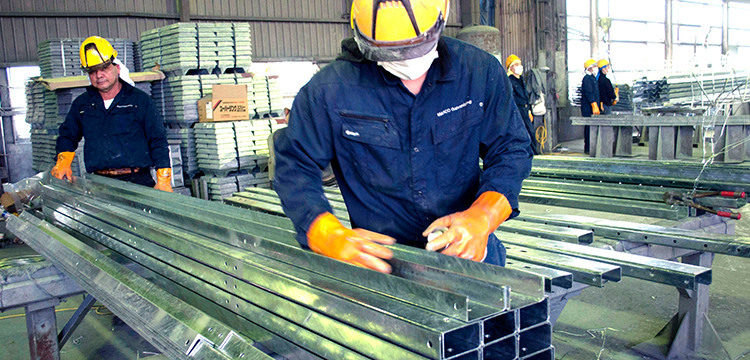

膜厚検査&外観検査
仕上げ後の品物の外観検査を行うと共に、専用の器具を使いメッキの付着量が規準値を超えているか検査します。

計測
仕上げ後の鋼材の外観チェック・数量チェックを行うのに加え、台貫にて重量を計測します。
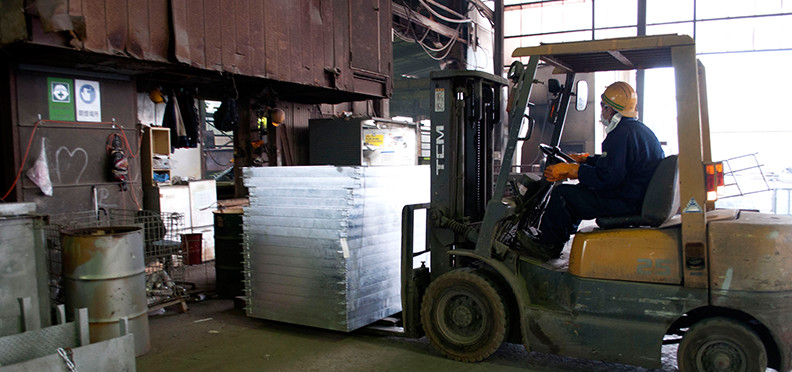
短納期の理由
一連の工程は、品物にもよりますがトータルで半日ほど。
工場の24時間稼働に加え、2012年より生産管理にiPadを導入したことで、品物がどこにあるかをリアルタイムで確認しながら作業できるようになり、作業効率が飛躍的にアップしました。今後は、生産管理だけでなく、製品状況をお客様に確認いただけるよう、流通面での “見える化” にも尽力していきたいと考えています。
メッキ窯サイズ
弊社のメッキ窯は最大11メートルまでの大きな商品もメッキが可能です。下図はメッキ窯の詳細になります。
溶融亜鉛メッキとは
溶融亜鉛メッキとは、雨風に常にさらされる街頭ランプや屋外設備の鉄部分など、我々の身近にある鋼材を腐敗から守る、優れた防腐処理のことです。
亜鉛とは?
亜鉛は、青味を帯びた光沢のある銀白色の金属です。融点は419.5 °C、沸点は907 °Cと、金属としては比較的低く、比重は7.14となります。通常、亜鉛は銅や鉛といった鉱石の中で、ベースメタルと一緒に産出されます。大規模な鉱床はオーストラリア、カナダ、アメリカなどです。
亜鉛は、我々の身近なところに使用されています。たとえば、酸化させて粉状にした(白色の粉末状)ものは、化粧品や車のタイヤなどに使われているのです。
溶融亜鉛メッキは、メッキ工法のひとつです。
亜鉛には、湿式製錬法(電解法)で製造した「電気亜鉛」と、亜鉛を還元する乾式製錬法で製造した「蒸留亜鉛」などがあります。
1、電気亜鉛メッキ → 電気を介した溶融液の中に鋼材を浸すことで、メッキ皮膜を作る処理法のことを指します。
2、溶融亜鉛メッキ → 高温で溶かした亜鉛に鋼材を浸漬し、メッキ皮膜を生成する処理法のことを指します。
マルコ工業では、優れた防食効果のある「溶融亜鉛メッキ」を取り扱っております。
溶融亜鉛メッキの歴史
フラックス処理を用いた溶融亜鉛メッキの始まりは、パリの土木技術師によって1837年頃に確立されたとされ、その後、ヨーロッパ各地に溶融亜鉛メッキ工場が広まっていきました。
日本における溶融亜鉛メッキの始まりは、1883年(明治16年)。1882年にイギリス人技術師の指導により、新橋~横浜間に始めて鉄道が開通したとき、汐留にあった東京電通局の構内で、通信用鉄線への亜鉛メッキを行ったのが始まりとされています。その後、徐々に溶融亜鉛メッキは国内でも工業化されていきました。
電気亜鉛メッキと溶融亜鉛メッキの違い
電気亜鉛メッキとは
鋼材を亜鉛メッキ液に浸して電解することで、メッキ皮膜を生成させる工法のことです。鋼材を、サビや腐食しにくくします。皮膜は薄く、おおよその膜厚は2~25μm。均一に付着できるのが特徴で、仕上がりが美しいため装飾品などに向いており、電気を通すものにも電気亜鉛メッキが適しているとされます。
溶融亜鉛メッキとは
高温で溶かした亜鉛の中に、鋼材を浸すことで亜鉛を付着させる工法のことです。溶かした亜鉛を槽に入れ、鋼材を浸していく様子から「ドブづけメッキ」「てんぷらメッキ」と呼ばれています。おおよその膜厚は、49~100μmと、厚みのある皮膜が生成できるため、耐食性に優れています。ガードレールなどの道路設置物、屋外設備機器といった自然環境の厳しい場所で活躍しています。
溶融亜鉛メッキの優れた点
溶融亜鉛メッキを施した鋼材には、サビ・腐食が発生する事はほとんどありません。さらに、塗装や電気亜鉛メッキ法と違い、合金層と呼ばれる層が亜鉛と鉄との間に発生するため、亜鉛と鉄が強力に結合し、長期間メッキが剥れることもありません。
また、溶融亜鉛メッキには、「保護皮膜作用」と「犠牲防食作用」があり、より強い防食性を生み出します。
保護皮膜作用・・・亜鉛メッキの表面に発生する亜鉛の酸化皮膜が、空気や水を極力通さない安定した性質を持っているため、サビを防いでくれる作用のことです。
犠牲防食作用・・・万が一、傷が付き下地の鉄が露出してしまったとしても、傷周囲の亜鉛が、鉄より先に溶け出し、電気化学的に保護するため、鉄を腐食から守る作用のことです。
この2つの作用により溶融亜鉛メッキは、優れた防食効果を発揮します。
マルコ工業では、「高品質・短納期」にこだわった溶融亜鉛メッキ加工を行っております。
こんなところにも使われている!溶融亜鉛メッキの用途について
鉄鋼をサビやキズから守る溶融亜鉛メッキは、ふだん皆さんが利用しているさまざまな設備・施設で使われています。駅や道路、発電設備でも目には見えない部分で力を発揮しているのです。安心・安全を支えている縁の下の力もち、溶融亜鉛メッキ。具体的にどのような使用例があるのかご紹介しましょう。
厳しい自然環境の現場で使われている。
鉄塔などの電力通信設備、発電所、河川付近や沿岸、山中、高所といった、
人が入りにくくメンテナンスがしづらい場所など。
たとえば、雨風の影響を直接受ける屋外の鉄塔や、ソーラーパネルの骨組み部分にも、溶融亜鉛メッキの力が活かされています。キズが発生しても、鉄に腐食が起きる前に亜鉛が解けて鉄を保護するため、万一の腐食を防ぐことができます。密着性にも優れているため、環境差はありますが剥離することはめったにありません。そのため頻繁なメンテナンスが難しい高所や山の中の送電網、橋、河川付近の設備、落石防止ネットなどにも使われ、施工後はほぼノーメンテナンスで長期に渡り使用できます。
大型サイズや、特殊な型の鉄鋼製品にも対応できる。
空港、鉄道、駅、競技場、市場、などのすべての鉄鋼製品
メッキ槽に浸漬することが可能な鉄製品は、すべてメッキ加工することができます。弊社の場合、最大11メートルの大型製品までメッキが可能です。また細長い管のようなものや、中空体なになっているもの、手の届かない部分があるものも均一に加工できます。断面が複雑な形になるエクスパンドや、様々な加工形状のものに対応しています。
また、少数、小ロッドや試作品などにも対応しておりますので、まずはお試しください。鉄を加工する前にご相談頂ければ、どの様な加工形状にするとより綺麗にメッキを施すことが出来るかをアドバイスさせていただきますので、お気軽に弊社営業担当までご相談ください。
施設、設備の長寿命化に貢献している。
駅舎、道路、公園などの公共施設、オフィス、駐車場など
設備の老朽化を防ぎ、耐久性に優れたる溶融亜鉛メッキは、皆さんが普段利用している駅や道路、公園などの公共施設や、オフィス、駐車場など、長期間の耐久性を求められる場所でも活躍しているのです。長寿命化にも貢献し、安心して使用できるよう見えないところで支えています。
例えば、最近良く見かけるようになった駅のホームドア。あのホームドアの下にはドア本体を支えるための鉄骨がホームのコンクリート内に埋め込まれています。その鉄骨も溶融亜鉛メッキを施し、腐食を防いでホームドアの長寿命化に貢献しているのです。
高温や湿気の多い場所でも活躍している。
プール、温室施設、園芸ハウスなど
サビが発生しやすい高温多湿な設備にも、溶融亜鉛メッキが施されています。表面にできる亜鉛の酸化被膜が、空気や水を通しにくい安定した性質を持っているため、高温多湿な環境であっても、サビから鉄鋼を守るのです。
例えば外と中の温度差の激しい農業ハウスや雪深い地域の建物や倉庫などにも幅広く利用されています。
ほかにも、溶融亜鉛メッキは道路のガードレール、橋、歴史的建造物補修など、ありとあらゆる鉄鋼を見えない部分から支えています。強い耐久性や、施工後の扱いやすさは結果として経済的にも優れた加工です。また、鉄鋼製の寿命を延ばし回収後の再利用もできるため、環境に優しい加工手法としても注目されているのです。
このように耐久性、経済性、環境性にも利点が多い溶融亜鉛メッキは、皆さんの周りのお困りごとを、縁の下から支えられる加工法の1つです。ぜひ一度、当社までお気軽にお問い合わせくださいませ。常に新しいことに挑戦するマルコ工業の専門スタッフが、お客さまのニーズにお応えできるよう全力を尽くさせていただきます。